在制造领域,复杂零件的加工精度与效率一直是衡量技术实力的核心指标。传统加工方式常因设备限制,需多次装夹、多工序切换,导致加工周期冗长、精度波动大。而龙门五面加工中心凭借其五轴联动技术,以“一次装夹、五面加工”的革新理念,正重新定义复杂零件的制造标准,为航空航天、汽车制造、精密模具等行业带来变革。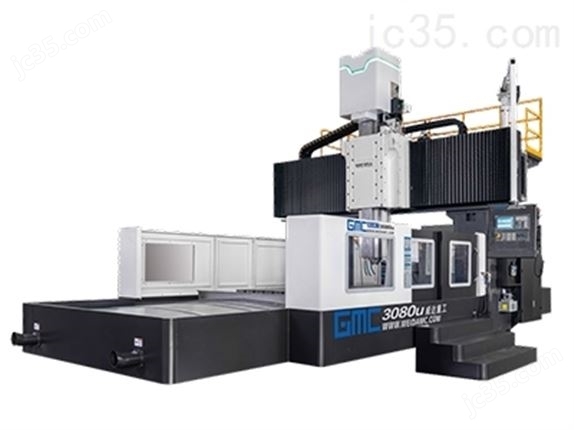
五轴联动:突破传统加工的维度局限
传统三轴加工受限于平面运动轨迹,难以高效处理复杂曲面、深腔结构或异形零件。而龙门五面加工中心通过A/C轴旋转与X/Y/Z轴直线运动的协同配合,可实现空间内任意角度的刀具路径规划。例如,在航空发动机叶片加工中,五轴联动技术能精准贴合叶片的复杂型面,避免传统工艺中因多次装夹导致的累积误差,将加工精度提升至微米级。这种多维度的加工能力,不仅提升了零件的几何精度,更保障了其动态性能与使用寿命。
高效集成:一次装夹,五面加工
传统加工方式需多次拆装工件以完成不同面的加工,这不仅增加了操作复杂度,更易因定位基准变化导致尺寸偏差。加工中心通过集成式设计,可在一次装夹中完成零件五个面的加工,大幅缩短加工周期。以汽车模具制造为例,传统工艺需数天完成的型腔加工,五面加工中心仅需数小时即可完成,且表面质量更优。这种效率提升不仅降低了生产成本,更满足了制造对快速响应与精益生产的需求。
重载稳定:支撑高精度加工的基石
复杂零件加工往往伴随高切削力与振动,这对机床的刚性与稳定性提出严苛要求。加工中心采用龙门框架结构与高精度线性导轨,配合大功率主轴与动态平衡系统,可承受高负载切削,同时保持亚微米级定位精度。例如,在钛合金零件加工中,设备能以高速切削去除大量材料,同时通过热补偿技术抑制热变形,确保零件尺寸一致性。这种“刚柔并济”的设计理念,使其成为高硬度材料加工的理想选择。
智能化赋能:从经验驱动到数据决策
现代龙门五面加工中心已融入智能化控制系统,通过实时监测刀具磨损、切削力变化等参数,自动调整加工策略。例如,设备可基于AI算法预测刀具寿命,提前规划换刀路径,避免非计划停机。此外,虚拟仿真技术可预先验证加工路径,减少试错成本。这种数据驱动的制造模式,不仅提升了生产效率,更推动了从“经验加工”向“智慧制造”的转型。
应用拓展:制造到通用领域
五轴联动技术的普及,使加工中心的应用边界不断延伸。除航空航天、汽车等传统领域外,其在医疗器械、新能源电池、3C电子等领域同样表现优。例如,在人工关节加工中,设备能以纳米级精度塑造关节曲面;在电池极片生产中,五面加工可实现极耳与极片的一体化成型,提升电池能量密度。
从精密模具到大型结构件,从实验室研发到工业化量产,龙门五面加工中心正以五轴联动技术为核心,推动复杂零件加工向高效、高精度、智能化方向演进。未来,随着材料科学与智能控制的进一步融合,这一设备必将在更多领域释放潜力,成为制造的“仪器”。